RAMMING MASS
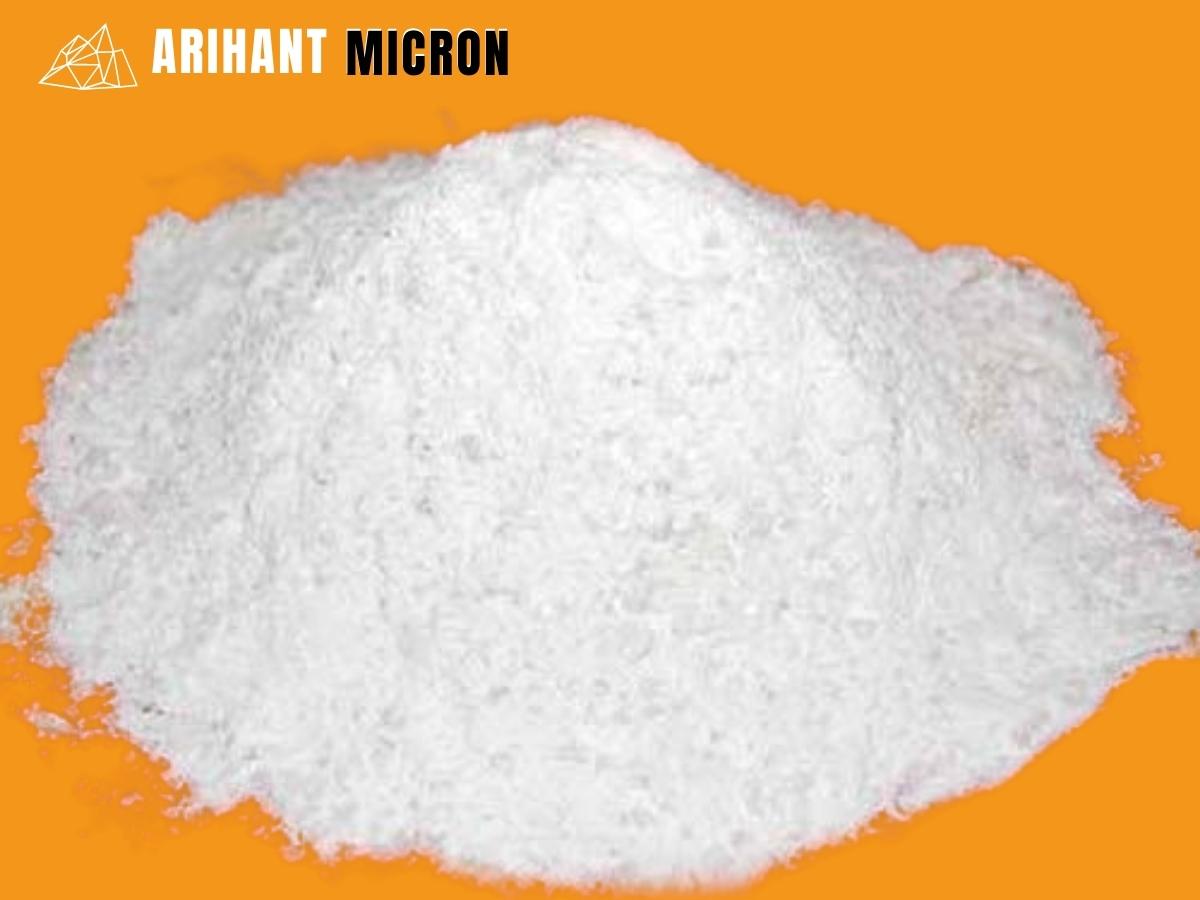
- ARIHANT MICRON is the best among the leading mining companies in terms of supplying high-quality quartz ramming mass, which is used as a refractory lining material for furnaces to prevent anti-coating, corrosion, and erosion. We manufacture 40% to 90% Al2O3-based ramming mass and 80% to 92% MgO-based ramming mass. Alumina Ramming Mass has a high alumina content and is widely used in industries such as nonferrous and ferrous, line and patching material for holding ladles, iron, and slag tapping furnace arch and roofs. It is also used in high-temperature applications such as metallurgical furnaces, the lining of rotary iron melting furnaces, and the repair of electric arc furnaces. Basic Ramming Mass contains high magnesia aggregates and is widely used in Induction and Arc Furnaces, among other things.
- Basic Ramming Mass, which contains high magnesia aggregates, is widely used in Induction and Arc Furnaces, among other places. It can be used to make high-quality alloys, as well as a mild and low-alloy steel. The basic ramming mass is composed of high-quality Dead Burnt Magnesite clinker combined with either Alumina or Chrome, which is then specially bonded with clay and other chemical binders to achieve the desired sintering characteristics. The specification "as per the table attached in a word file.
Granulometric composition of commercial silica ramming mass
5mm-1mm |
1mm-.20mm |
0.20mm-0.60mm |
0.60mm and below |
33% |
30% |
17% |
20% |
Basic Ramming Mass
Product |
Setting |
Sintering temp° C |
MgO % (Min) |
Fe2O3% (Max) |
Cr2O3% (Max) |
Rammed B.D at 110° C Min |
SiO2% (Max) |
CaO% (Max) |
Grading in mm (Max) |
Service Temp in° C |
Application area |
AM Mag Ram (IF) |
Chemical |
800 to 1200 |
70 |
3.5 |
8 |
2.40 |
6.00 |
2.5 |
0 to 5 |
1750 |
Medium to high-frequency induction furnaces making mild & alloy steel |
AM |
Chemical |
800 to 1200 |
85 |
1.5 |
1.5 |
2.60 |
8.00 |
2 |
0 to 5 |
1750 |
For special & manganese steel induction furnaces |
AM Mag Ram 84 |
Chemical |
1200 |
84 |
1.5 |
2 |
2.60 |
8.50 |
2 |
0 to 5 |
1750 |
For construction and repairs of steel operating basic slags (EAF) furnaces |
AM Mag Ram 87 |
Chemical |
1200 |
87 |
1.5 |
1 |
2.65 |
7.50 |
2 |
0 to 5 |
1750 |
|
AM |
Chemical |
1250 |
90 |
1 |
0.5 |
2.70 |
4.50 |
1.5 |
0 to 2 or 0 to 5 |
1700 |
AOD, Various apply in ferrous &nonferrous industries |
AM |
Chemical |
1300 |
94 |
1 |
0.5 |
2.80 |
1.50 |
1.5 |
0 to 5 |
1750 |
Ramming of Taphole of BOF, EAF, converter, etc |
AM MagFet |
Chemical |
1200 |
65 |
3 |
Traces |
2.40 |
10.00 |
2 |
0 to 5 |
1650 |
Fettling of slag line of EAF Tundish Coating, Steel launder coating patching of slag line of a steel ladle, etc |
Neutral Ramming Mass
Brand |
Al2O3% (Min) |
MgO % (Max) |
Fe2O3% (Max) |
Rammed B.D at 110° C (Min) |
Setting |
Grading (mm) |
Sintering Temp °C |
Service Temp °C |
Application Area |
AM-TD-Ram-40 |
38 to 40 |
20 |
2.5 |
2.00 |
Air |
0 to 5 |
1100 |
1500 |
Non-Ferrous Industries |
AD-TD-Ram-70 |
68 to 70 |
20 |
2.5 |
2.5 |
Chemical |
0 to 5 |
1100 |
1650 |
For High temp application in steel plants |
AM-TD-Ram-EAF |
60 to 65 |
18 to 20 |
2.8 |
2.45 |
Air |
0 to 5 |
1100 |
1650 |
EAF |
AM-TD-PLAST-90 |
88 to 90 |
12 to 14 |
1.0 |
2.75 |
Chemical |
0 to 5 |
1200 |
1750 |
EAF |
Acid induction furnace linings have mass ramming. The heating performance of the furnaces is directly related to the acidic ramming mass quality. Better lining quality leads to smoother furnace operation, higher output, and improved metallurgical control. It is manufactured under the close supervision of a skilled and experienced workforce. A magnetic process is thoroughly tested to ensure iron-free material and proper granule composition in accordance with furnace capacity. The mix is granulated with the furnace's make and capacity in mind, yielding maximum and best results. It has higher thermal stability, corrosion resistance, and wear resistance than plastic because it contains fewer binders, fire clay, and moisture.
Features
- Pure
- Meticulous and organized lining ability
- Long shelf life
- Usage of best quality material
- Consistent performance
- Wear resistant
- Optimal bulk density
- Free from sintering agent
Used In
- Metallurgy
- Furnaces
Product Specification
- Proper mixing of binder leads to the optimum mixture.
- Less wastage, as mixing is done by machines.
- Imported Boric Acid is used to give the best results.
- Consistent and longer lining and patching life.
- One less item in inventory.